This is the story of the hunt for people who can fix all this old gear, people who really KNOW it inside out. And it’s also about what can be done about the slow but steady loss of this deep knowledge and real, hands-on experience from the world of vintage audio. And yes, it does also at least attempt to answer the question: “can you fix my….?”
Are you a tech looking for work reading this? Or maybe you want to learn (and are local to us)? More info below, but we definitely want to hear from you!
The Quest for Techs
The toughest part of this business has always been finding the right technicians to service and repair the wide range of gear we handle. Going back to when I was just hunting down gear for my studio, there was always a shelf/wall/cupboard or two stacked with ailing and decrepit pieces that I’d bought out of curiosity (most often in the optimistic hope that ‘untested’ meant ‘working’), and then kept in the hope of finding that special someone prepared to spend time tracing circuits and fixing the obscure stuff that nobody else would touch.
Along the way I found some generous and clever guys (yes, they were always guys) with zen-like abilities to fix the unfixable and who delighted, as did I, in resurrecting these arcane devices. Then there were the less than genius types: some started well with reasonably-priced initial work of a fair standard, then steadily decline over time as their bills increased; others would take my precious pieces into their lair and weave intricate myriad fables and falsehoods into tangled webs of deceit and denial until I could stand it no more. There were the good, the bad, the ugly, and the downright crazy.
What I’ve learned along the way is that precious few technicians allow themselves to refuse work, and I find it refreshing and encouraging to meet those who clearly state what work they will and will not take on, and who run efficient diaries. With vintage gear, it is nigh on impossible to predict how long a particular service/repair will take, and it is to technicians’ credit that they ever attempt to do so. It is all too common to commence with a seemingly-simple fix that should take an hour or two to complete, to then find oneself under a collapsing house of cards that becomes days of work that cannot be reasonably billed for.
I consider myself very fortunate to have worked with some truly gifted and generous individuals, who’ve enriched my life considerably, and enabled me to indulge in my passion for weird, wonderful and sometimes just plain strange music gear. As a result, one of the biggest joys for me of running Soundgas is knowing that pretty much everything we find, no matter how obscure or seemingly beyond repair, can in fact be resurrected: you just have to find the right tech for the job (and secure the space in his diary).

Brain Drain
As Soundgas grew and expanded into new areas of gear, so too did our network of willing and able technicians. Yet, as time has passed, it’s become increasingly-apparent to those of us who live and breathe vintage gear that the rate of attrition in experienced and competent engineers has been terrible. As I’ve highlighted above, it’s impossible to predict how long many repairs will take, or even to know if they’ll be successful, and often the honest technician must choose between disappointing their customer, or working at greatly-reduced rates to deliver a promised repair. Many work very long hours in solitude, and the pressures of running a business, combined with customers’ unreasonable expectations, take their toll.
Initially it was the techs specialising in older technology, such as valve gear, that started to vanish, then it was those who worked with tape, now it’s synths and effects. Modern electronic equipment is rarely built to last, nor to repair, and in a world where disposal and replacement is the standard, who now serves old-style apprenticeships in TV and radio repairs, or musical instrument shops? The new cheap, disposable technology imported from afar comes at a high cost to our future.
We realised that we would not be able to continue supplying our customers with high quality vintage gear unless we could also ensure its future maintenance. From conversations with our customers, it’s become very apparent that there is an international shortage of experienced, qualified technicians able to look after the gear we all love and use on a daily basis. We feel that we would be failing in our duty of care to our customers if we did nothing to reverse this decline.
We have already lost so much knowledge and expertise in industries where skills were passed down from generation to generation without the information being formally recorded. A sad example is the Mullard valve factory in Blackburn: at the height of their success they employed 6,000 people. Mullard valves are now belatedly-recognised as being superior to those manufactured today - we see gear that will only function correctly with a Mullard or similar vintage valve - new ones are not up to the same standard. Mullard’s technical wizardry is now lost: the machinery was exported to new locations abroad, but without the inherited knowledge and skillsets passed down through the workforce, the products being produced are not in the same league.
We cannot allow this to happen in our industry. The solution is investment in training the next generation of techs so that no more hard-won and irreplaceable knowledge is lost. This is time-consuming and expensive, but it is absolutely-essential that we take this on. We started a year ago, and are increasing our efforts to make this happen. When you buy from Soundgas, you are supporting this work and helping to ensure the future of your vintage equipment.
It is our mission to help educate and inspire the next generation of technicians.
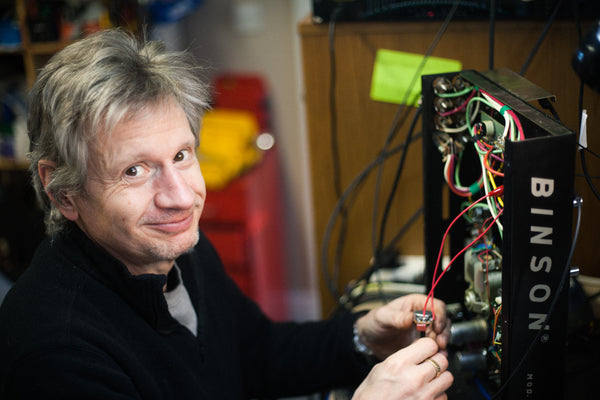
Future Proofing
When our indomitable independent echo tech, Doctor Huw, mentioned that if he performed much more work for us he’d risk his self-employment status, the spark of an idea formed that lead to the opening of the Soundgas Service Department just over a year ago.
Doctor Huw is an exceptional echo technician - the best I’ve had the pleasure of working with - and his commitment to quality has been a major factor in Soundgas’ success.
Doctor Huw’s brief was to help us train new technicians, while still keeping the wheels turning at Soundgas. We were fortunate to find his first apprentice, Max Dawson, who proved so able that we swiftly removed him from the Government Apprenticeship scheme and offered him a full time position.
Read more about Max and Huw here.
Huw and Max are doing sterling work, and BBC-trained Huw is now schooling Max in the various dark arts of tape echo maintenance and electronic repairs and servicing. We aspire to offer repairs and servicing to all, but for now the Service Dept are fully-engaged with our own work, and servicing gear that we have previously sold to customers (if you buy from us then we will always endeavour to help maintain your purchase). The immediate benefit to our customers is increased efficiency and wider availability of fully-functional serviced and guaranteed vintage gear, and the knowledge that we are working towards ensuring our ability to maintain that equipment.
We are one of just a handful of companies in the world working to train new techs and ensure that the knowledge and experience of previous generations is passed on and safeguarded for the future. When you buy from us, you are supporting the education of future technicians.
Onwards & Synth-wards
Synth repair and restoration has long been an Achilles Heel for us at Soundgas; there are so few good synth techs with the required breadth of experience and knowledge (and who share our passion and commitment to excellence) to work on the wide range of vintage synths that we see. It is very clear that, as with valve and tape technology, there are no provisions being made for the future maintenance and repair of these instruments.
For many years we've worked with our good friend, James Walker - an exceptional tech with unparalleled knowledge and experience - and he has been a constant source of inspiration and assistance to us as we’ve expanded. Without James’ advice and abilities, many otherwise unsaleable synths and effects would have been consigned to the scrapheap (or parts shelves) and I would never have discovered some of my favourite pieces. James is unwavering in his determination to see a job to completion, though this can sometimes come at a high personal cost to him both financially and healthwise. He has an uncanny ability to repair pretty much any synth we throw at him (or rather hand him carefully).
We have been working ever more closely with James as we collaborate on a plan to share his deep knowledge more widely. We are very excited to announce that from June 2018, James is going to join us at Soundgas and help train and and educate new synth technicians. He will also be continuing his work in the Soundgas Service Department which will allow us to handle synth repair work in future. We plan to work together to build an online resource of information, demos, “how tos” and schematics to assist and enable people to maintain and repair vintage synths.
And we've been incredibly fortunate to secure the services of Chris Challoner, who joined us on a part time basis before Christmas and who has swiftly become an integral member of the Soundgas family. Chris is something of a renaissance man and a supremely-talented individual (as well as being an all-round nice guy) and is the only member of the Soundgas team to have featured on Star Wars’ credits. Chris will be working closely with James Walker in our synth service department.

So, that's all great, but
Can you service my gear?
While we aspire to open our service department to all, this is not something that can happen quickly. Our immediate commitment is to our customers and to training new technicians. If you buy a piece from Soundgas, we will do our utmost to assist you with any future maintenance or repairs, wherever in the world you may be.
Our future plans include investment in the service department and the training of technicians so we will be able to efficiently assist with repairs and servicing in future. This is an ongoing process, and we hope to be able to help in the very near future.

Want to join us on this journey into gear?
Experienced Techs & Apprentices Wanted
We are working to bring together an approved list of technicians who we can recommend to our customers both in the UK and worldwide. If you wish to be considered for inclusion in this list, please email us with details of your business, specialities and experience.
We are seeking experienced technicians of any age to work with us on a range of equipment, and also we are now looking for an electronics apprentice - ideally school leaver age. Please get in touch if you wish to join us or work with us remotely.
==========
Tony Miln is the co-founder (& Head Gear Head) of Soundgas. See/hear him in action on Instagram.